
End-to-end solutions for battery minerals extraction, refinement, and recycling processes
Digital tools (Geminex™) for adapting operations based on variability in ore bodies
Proprietary technology with broad industry know-how and delivery capabilities
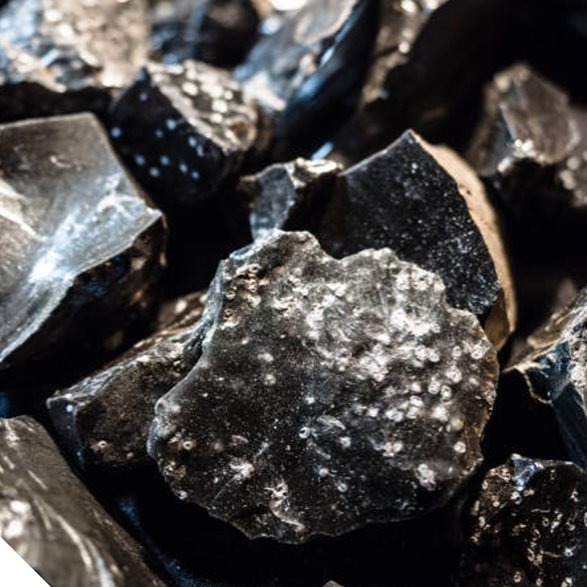
Key drivers for battery minerals industry
The growing adoption of electric vehicles is driving rapidly increasing demand for rechargeable batteries and their input commodities - including lithium, cobalt, nickel, graphite, manganese, copper and aluminum.
As society continues to embrace batteries as the more responsible alternative for burning fossil fuels, we need to accept that we can’t just concentrate on the sustainability of individual end user commodities such as EVs. To determine and improve sustainable performance, we need to take a holistic approach and lead the way towards a more responsible overall business ecosystem.
Introducing Metso in Battery Minerals

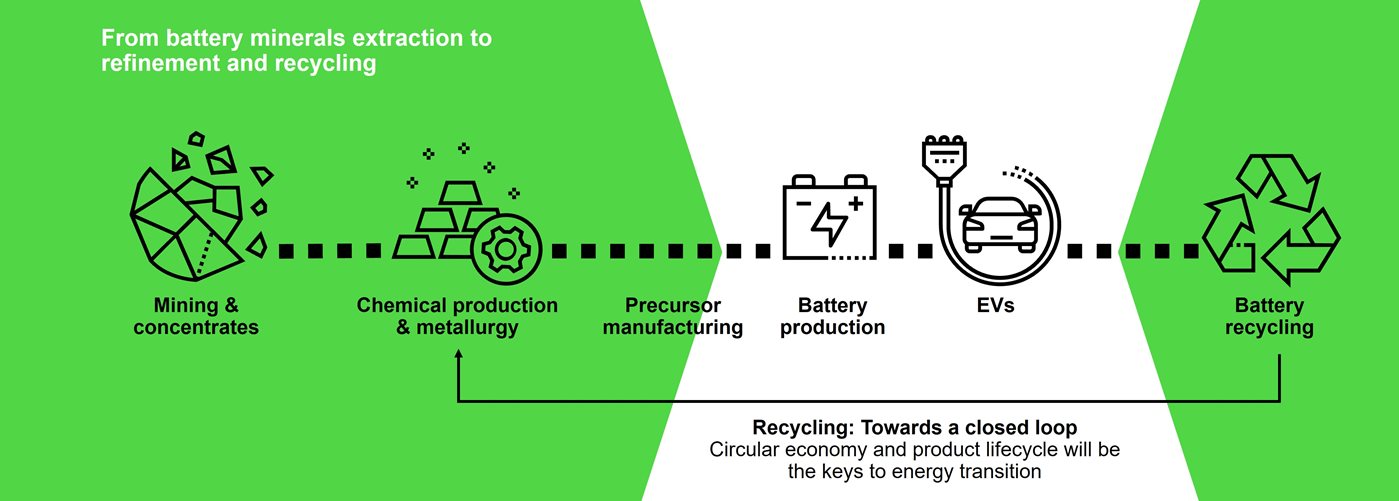
Multiple minerals and processes
Brines – Hydrometallurgical processing

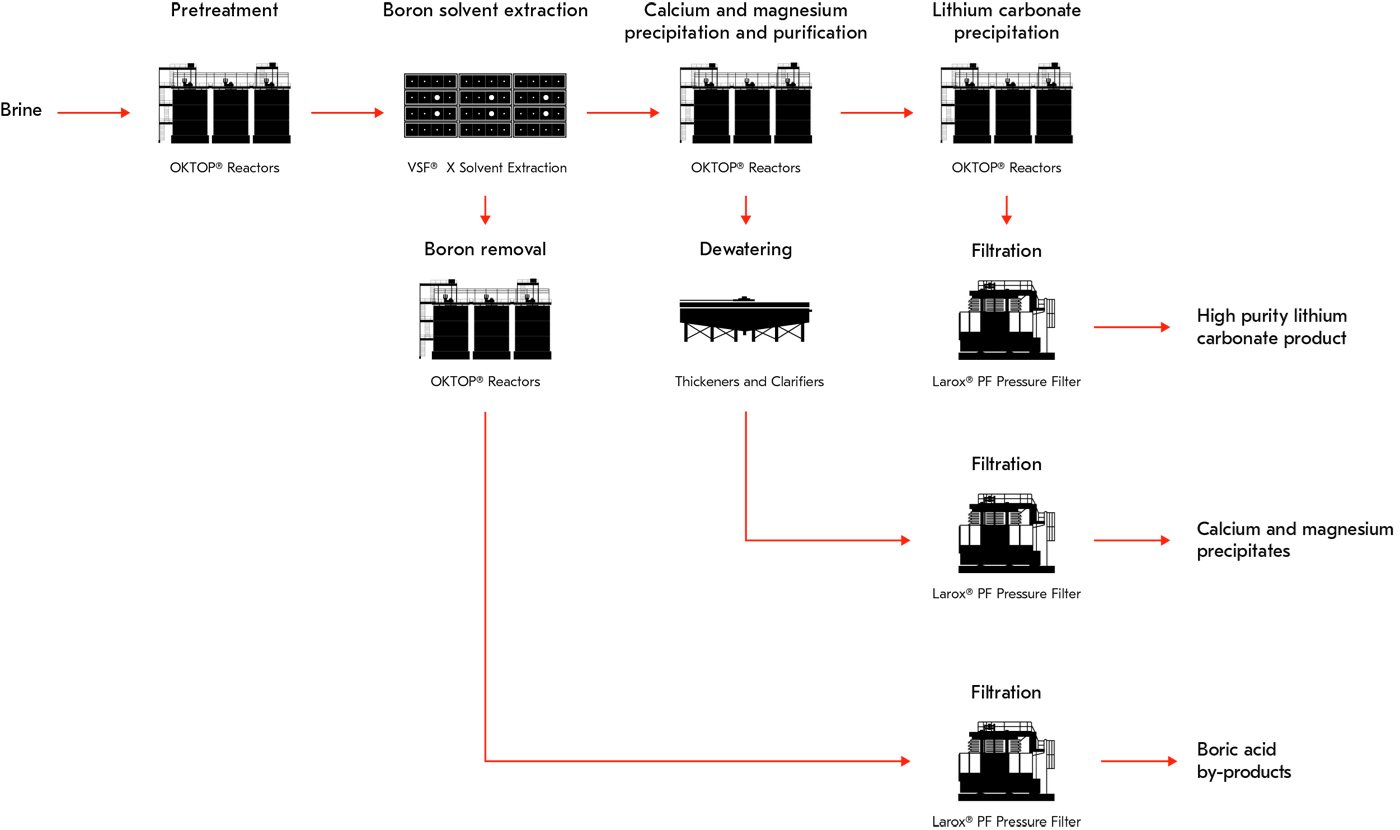

Spodumene – Concentrator plant and hydrometallurgical LiOH process
Metso provides the path to optimized solutions and complete plants for the production of high-purity lithium salts. Our innovative and proven calcination, leaching, purification and lithium recovery technologies cover the whole range of production, from raw materials to battery grade lithium products: most importantly Lithium Hydroxide Monohydrate and Lithium Carbonate.
Metso’s proprietary technology offers a short-cut process concept for spodumene concentrates: direct alkaline leach process for lithium extraction and solubilization, followed by crystallization of the lithium salt product. Furthermore, the leach process is environmentally sustainable: acid & sulphate free, without undesired crystallized salts or by-products, producing inert & neutral mineral residue for re-use or disposal.
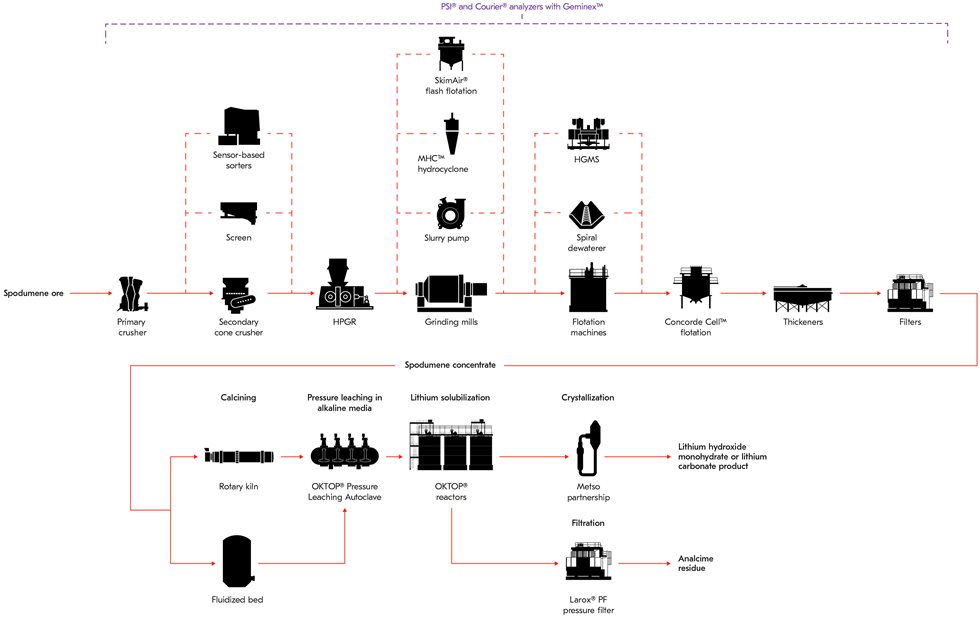
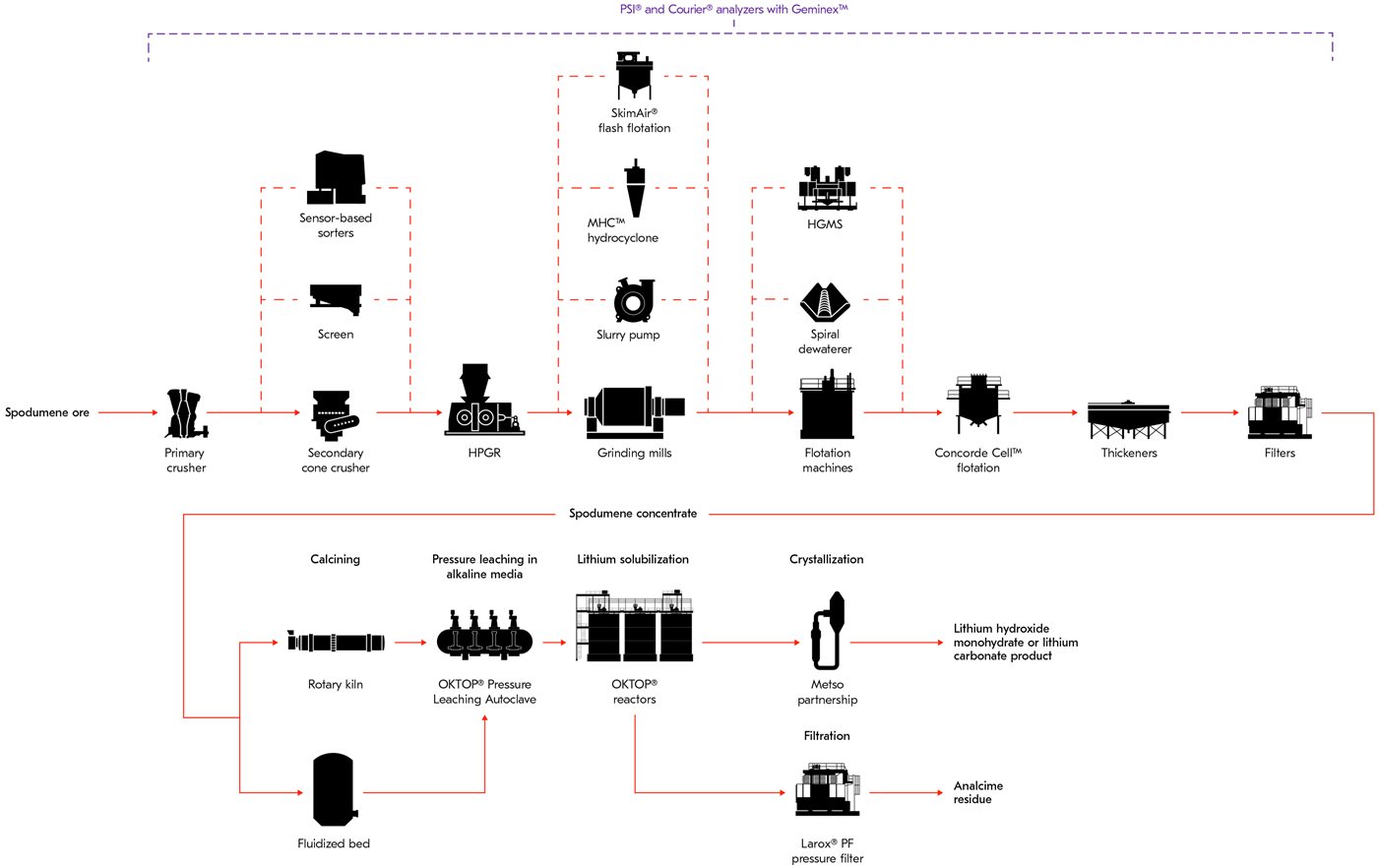
Nickel and Cobalt - hydrometallurgical processing
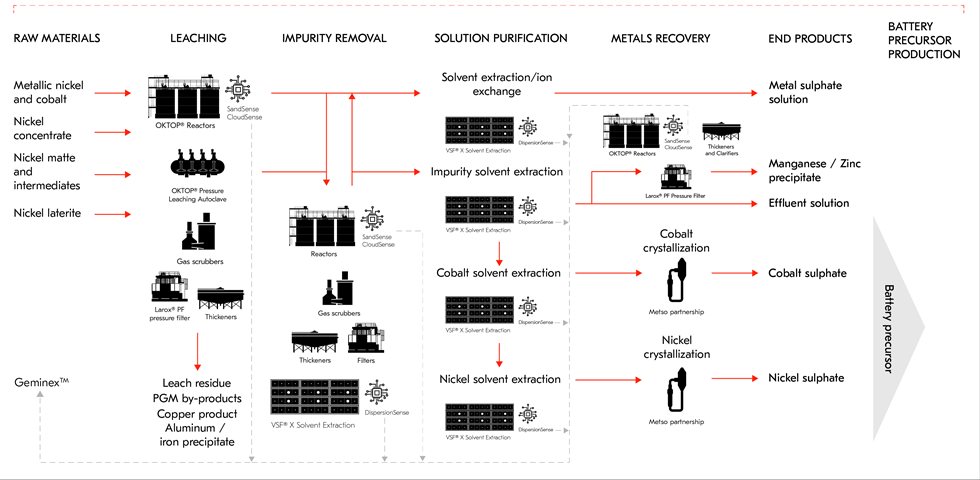
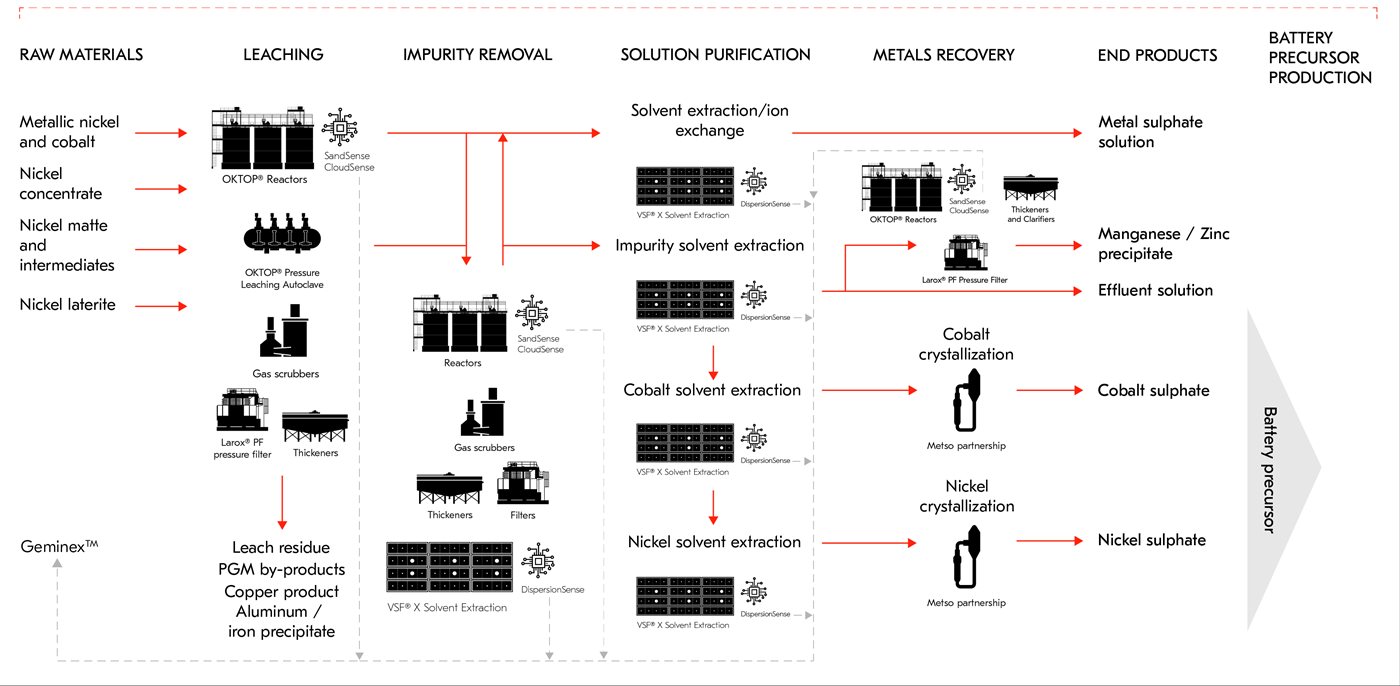

Black mass - Battery recycling process
The Battery black mass recycling process treats batteries after mechanical separation and optional thermal treatment for the recovery of nickel, cobalt and lithium, as well as optionally manganese and copper. The process flowsheet can also be tailored according to the feed materials and desired end products with possible phased approach, starting with recovering the most valuable metals.
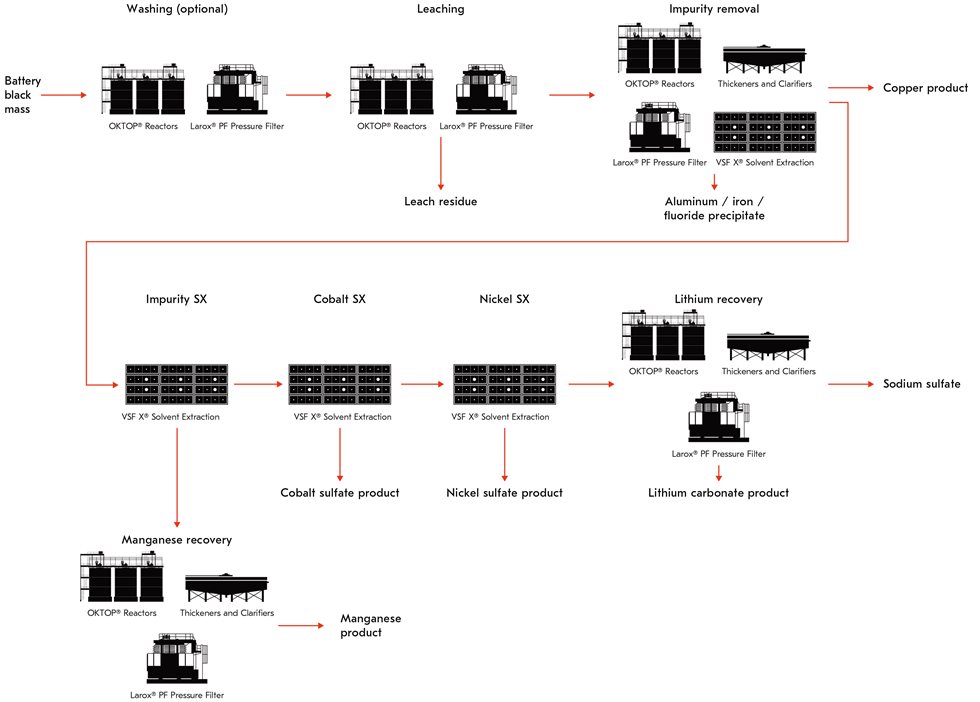
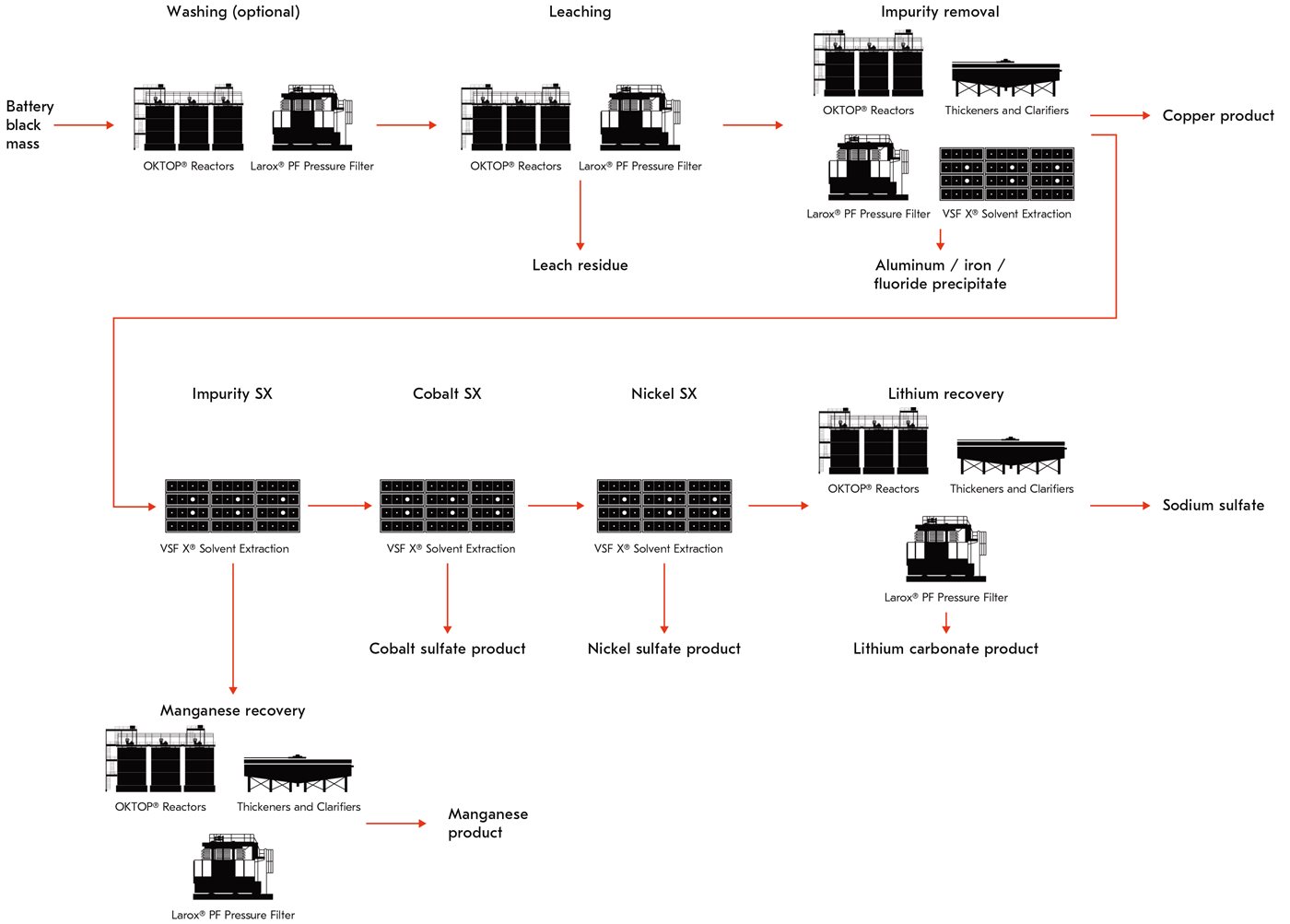

Metso pCAM plant
Centred around OKTOP® pCAM reactor, PSI® 1000 particle size analyzer, and pCAM process control, Metso’s pCAM plant integrates advanced technology and decades of know-how to ensure an energy-efficient and sustainable process. Backed by world-class research & and testing capabilities, Metso’s pCAM plant is an integrated solution for all co-precipitated chemistries.
Core attributes
- Proprietary technology including OKTOP® pCAM reactor, thickeners, filters, analyzers to form core of the process
- 1st western pCAM plant provider
- In-house process development, pilot and bench scale plants for testing
- Batch, semi-batch, and continuous operation with one reactor setup
- Low energy and water consumption with Metso technology
- On-line analyzers to ensure high production rate

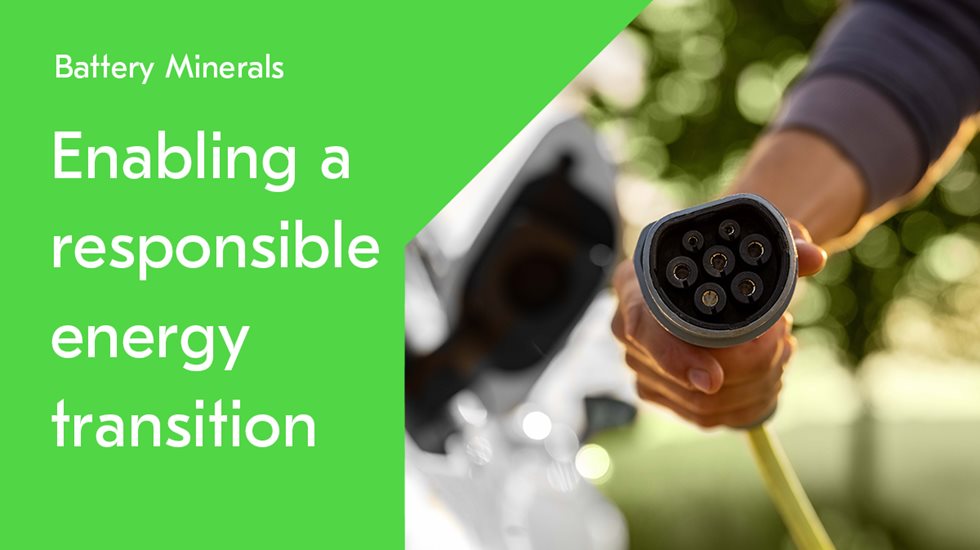