In recent years three-dimensional (3D) CAD has also been widely adopted in machinery design. An example 3D-model of an Outotec cathode stripping machine is presented in Fig. 1.
A novel method to optimize machine design using dynamic simulation – a robotic nickel starting sheet stripping machine case study


Dynamic simulation
While conventional CAD is a fundamental part of the mechanical engineering process, it has limitations in evaluating the dynamic behavior of equipment in operation. This is particularly important for demanding material-handling equipment such as Outotec cathode stripping machines. Outotec cathode stripping machine technology has utilized robots since 2010, which has significantly increased flexibility and capabilities in cathode handling. At the same time it has become essential to compare and optimize different layout options in order to realize the full benefits of the technology.
To overcome the limitations of CAD, Outotec has a novel 3D simulation method that simulates all individual machine units moving in relation to each other in real time. This model takes into consideration the dynamic behavior of different mechanical units, allowing the effect of dynamic forces and other mechanical constraints to be assessed realistically. This enables optimization and performance evaluation before the final design is fixed for manufacturing. A schematic diagram of the design process is presented in Fig 2.

One of the major benefits is that different concepts can be compared to find which one is the most optimal. Consequently, this procedure reduces the risk of modification during the assembly and factory-testing phases. The ultimate goal is to ensure that the equipment will achieve the high levels of performance and reliability that are critical for production.
Case example: A for Norilsk Nickel Harjavalta
In 2019, Norilsk Nickel Harjavalta (NNH) ordered a new nickel starting sheet stripping machine from Outotec to replace their nearly 30-year-old machine. The new machine had to provide fully automatic operation and flexible material handling of starting sheets and mother blanks. As the new machine is located on top of the existing machine in the tankhouse, it created several constraints regarding available space. Due to operational requirements, the machine had to manage the transfer of starting sheet stacks and mother blank racks between different floors without interrupting the starting sheet stripping process. In addition, the delivery time for the equipment was only seven months, which placed additional pressure on Outotec’s engineering team as they needed to develop a completely new machine based on the latest technology.

Outotec stripping machine design
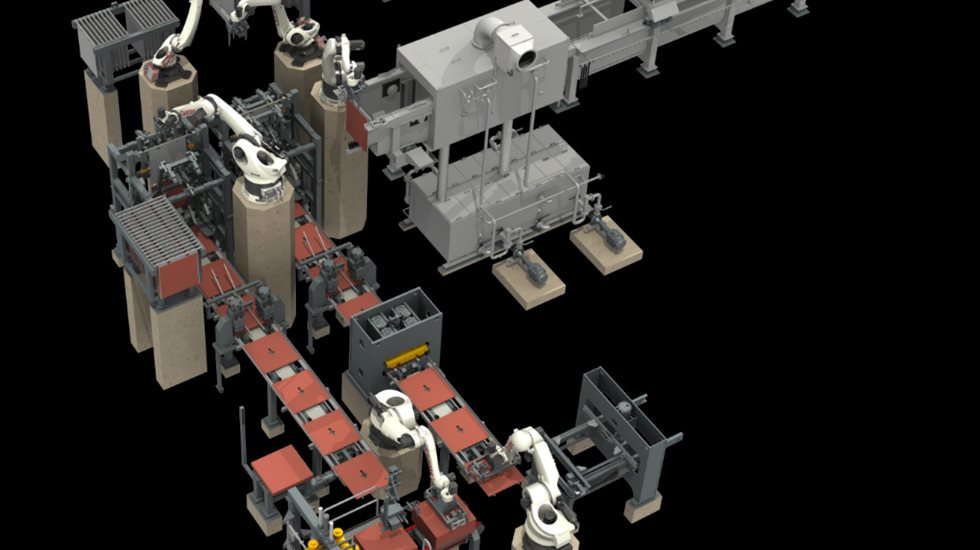
The machine’s operation was thoroughly tested during the factory acceptance test in March 2020 using material samples received from the customer (see Figure 4). The installation and commissioning of the equipment will take place later in 2020.
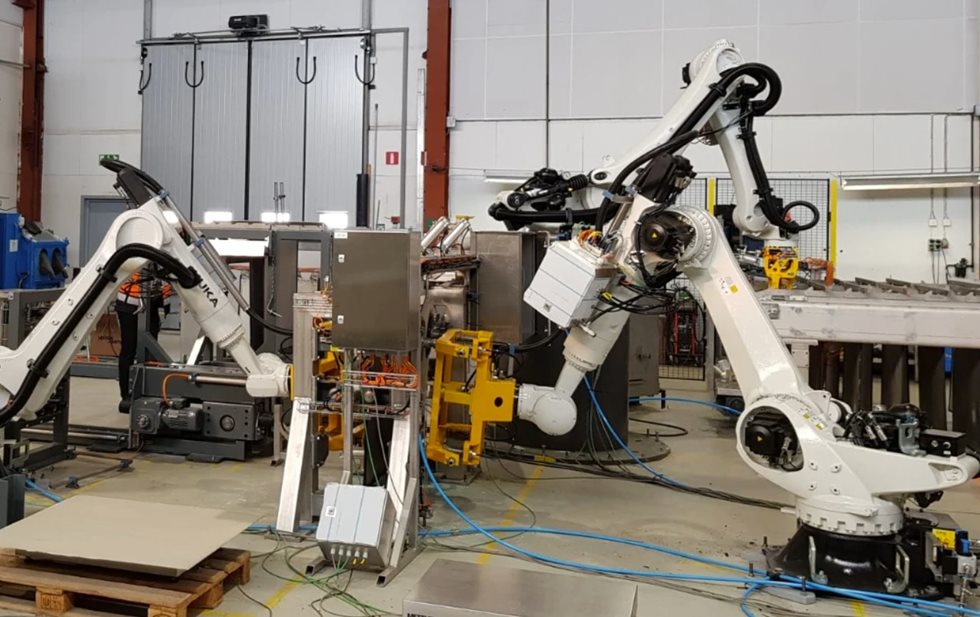