JK Sorajaloste, based in Jokioinen, Finland, recently electrified its crushing chain’s primary crusher with the acquisition of a Lokotrack® LT120E™ mobile jaw crusher with a diesel-electric drive.
JK Sorajaloste electrifies its primary crusher with Lokotrack® LT120E™ mobile jaw crusher
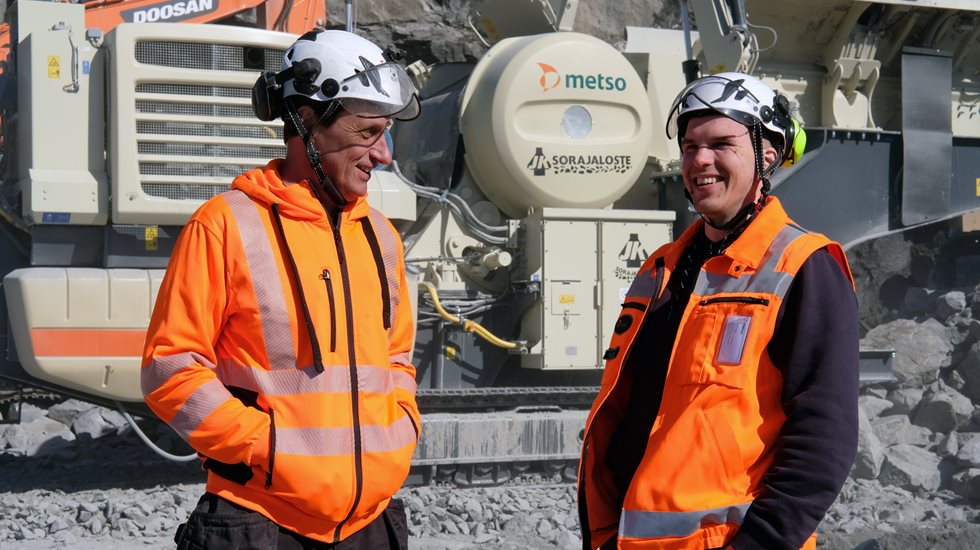
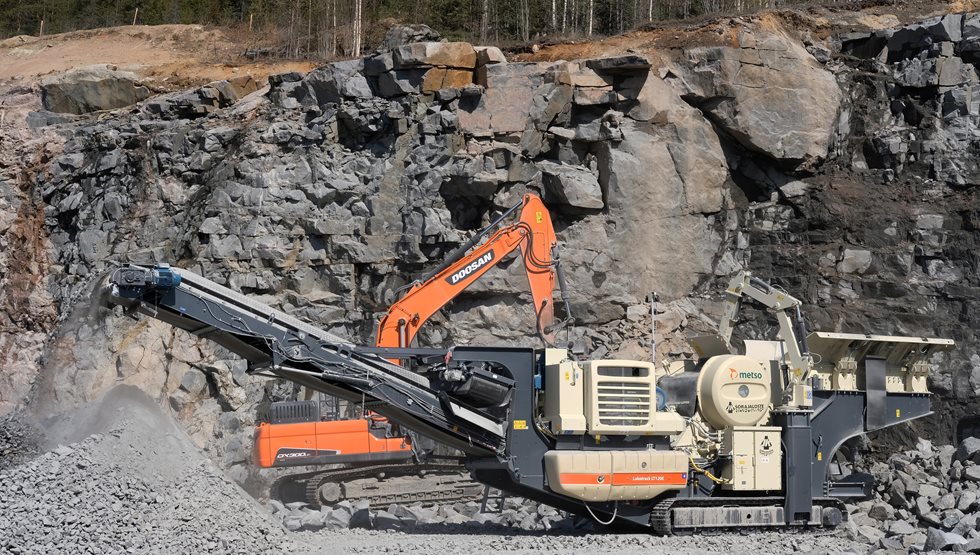
“An electric drive was an essential factor for us when choosing the new equipment, since our plant’s fine crusher and screen are fully electrically driven. In future, we’ll be able to run the whole chain using only one generator set,” says Jarmo Stenberg, one of JK Sorajaloste’s three entrepreneurs.
“We’re looking for economy and reliability with the electric drive. It’s certainly cheaper to transmit power electrically than with hydraulic oil. As a domestic manufacturer, Metso was the obvious choice: Spare parts and service can be found just around the corner in Tampere.”
“Electricity is also an environmentally friendly power source. We frequently carry out crushing operations in groundwater areas, where an electric drive is often the only permitted crushing method,” Stenberg adds.
First trial with a 50,000-ton contract in Asikkala
In April, the Tampere factory delivered the new LT120E to Asikkala, where its first trial was a 50,000-ton concrete gravel contract for Päijät Murske. The jaw crushing plant was fed with hard Class 2 rock.
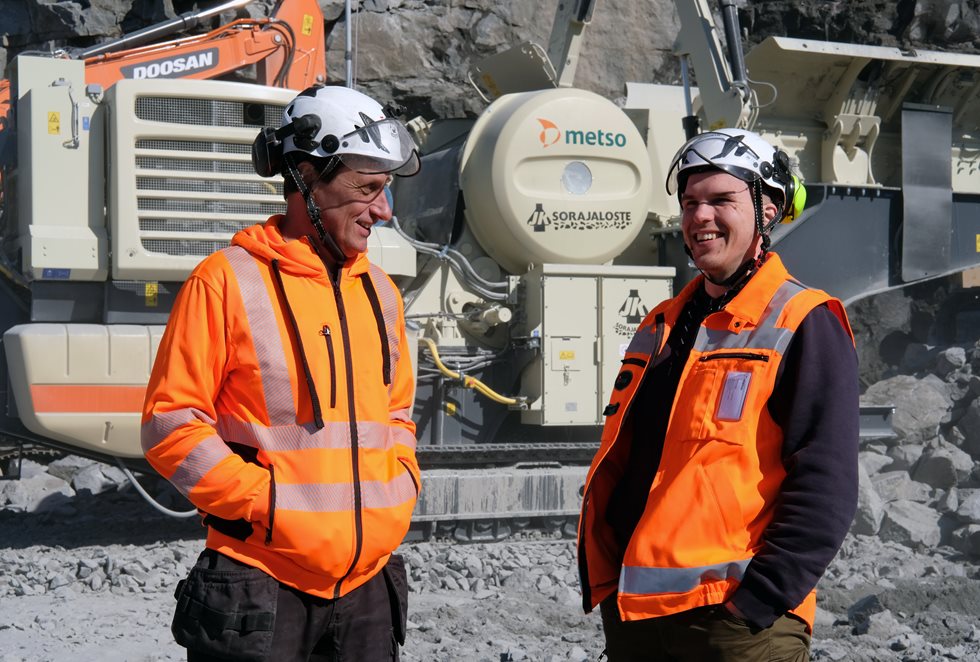
In this contract, JK Sorajaloste used an operating model familiar from Sweden and Norway, in which the primary crusher works as a separate unit, and the pre-crushed rock is moved with a wheel loader either to intermediate storage or directly for fine crushing and screening as required.
“This crushing method brings us reliability and flexibility. If, for instance, screen meshes need to be replaced in the secondary stage, the primary stage can be kept running. In the same way, the fine crushing stage can be fed from the intermediate storage while the jaw wear liners are being replaced,” Stenberg says.
Fuel consumption a little more than 20 liters
While crushing hard rock and even with an exceptionally tight setting of 100 mm, the fuel consumption of the LT120E has not risen much above 20 liters per hour. With these settings, approximately 3,000 tons of material are produced for the fine crushing stage during a 15-hour working day, i.e. about 200 tons per hour.
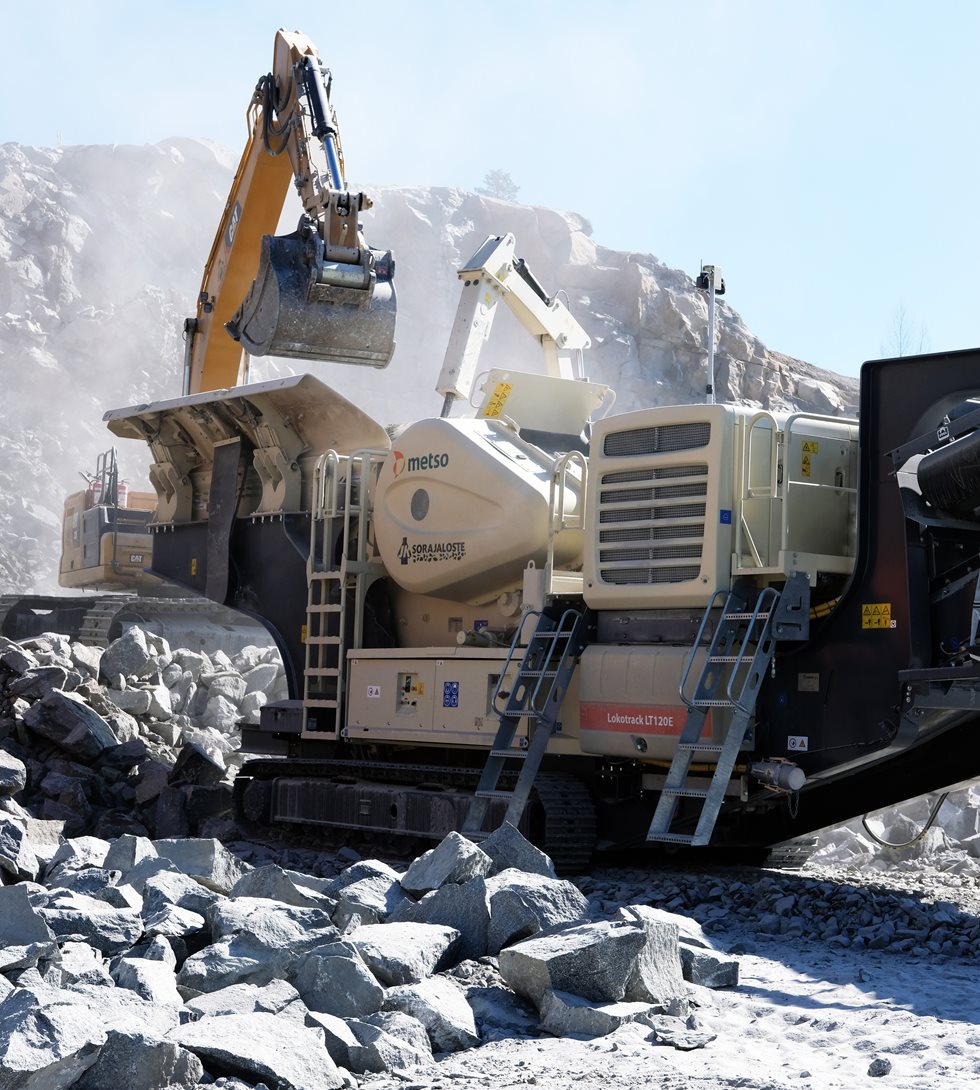
“We’re producing quite fine material with the jaw crusher, as this is best suited for the fine crushing stage. The LT120E could probably produce twice as much larger material,” Stenberg believes.
“Fuel economy has improved significantly over the years. Although we don’t have exact figures, the LT110C mobile jaw crusher we rented earlier was a lot thirstier than the new diesel-electric plant. The new diesel engine runs steadily at 1,500 rpm. The LT120E plant is roughly 15–20% more powerful than the old one, based on initial experiences.”
Jyrki Viitala from Metso’s technical support offered guidance for the commissioning of the new equipment, and area sales manager Mikko Luopio explained the benefits of the Metso Metrics remote monitoring system. JK Sorajaloste will be able to establish a satellite connection to the new equipment in the future when needed, and to see key data related to the crushing operation.
An expert in concrete aggregates
The Jokioinen-based JK Sorajaloste has developed its operations over the years, especially in the efficient production of concrete gravel. Most of the aggregates produced for Päijät Murske were sent directly to precast concrete element factories in the nearby region.
High-quality, cubic concrete gravel was produced in sizes of 0–6 mm, 6–12 mm and 12–18 mm. Aggregates of 0–8 mm, 8–16 mm and 16–32 mm were also produced.
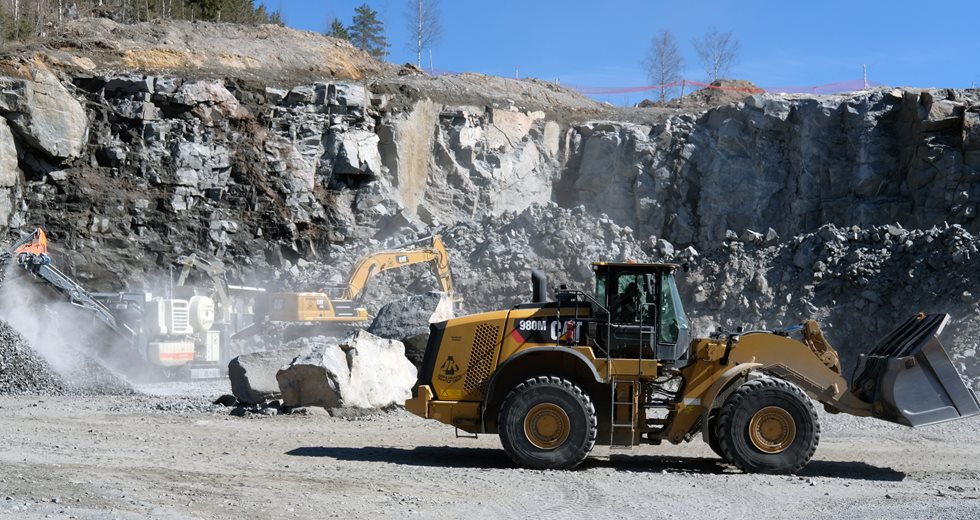
The company’s roots go back to the 1950s, when Jarmo Stenberg’s grandfather Leevi Stenberg started gravel sales and delivery operations in Lamminkylä in Jokioinen. JK Sorajaloste was adopted as Jarkir Oy’s business name, and the company acquired its own crushing plants in 2015.
Today, the company produces 600,000–650,000 metric tons of aggregates through contracts each year. The company also carries out various kinds of screening work in addition to crushing, delivering concrete gravel and fillers, among other products. The company has six employees.
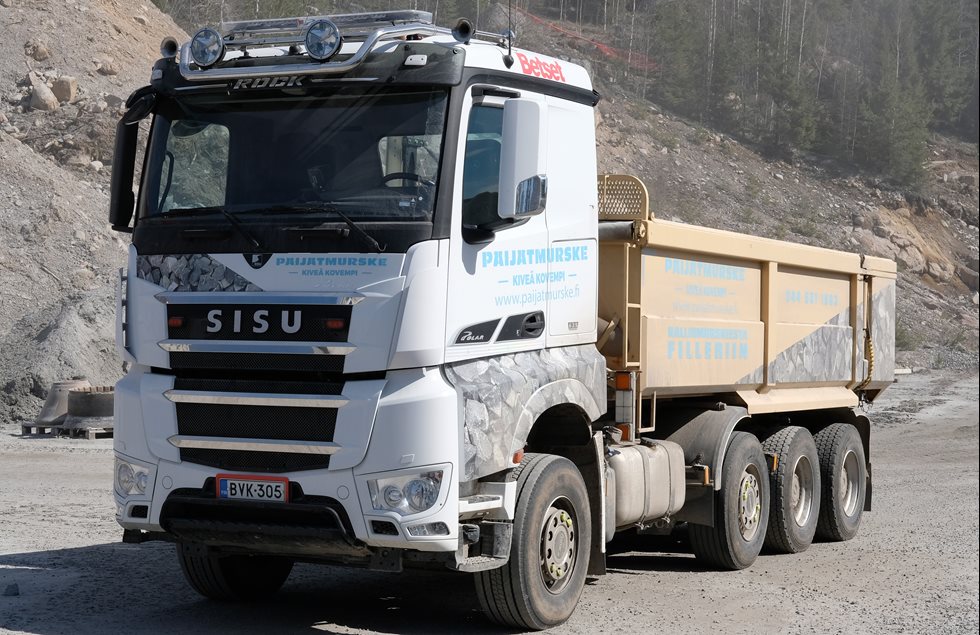