Get help with simulations of your equipment
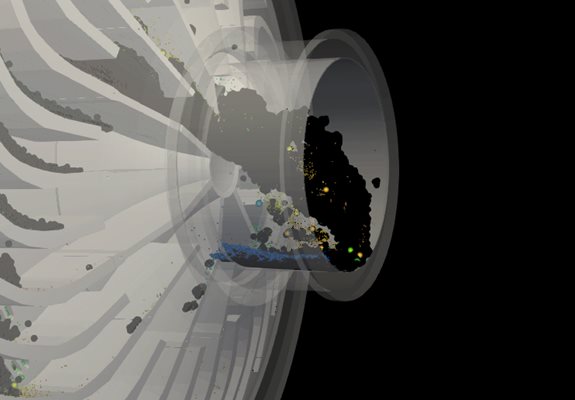
By using physics-based numerical simulation models combined with our minerals processing expertise we can improve the energy efficiency and performance of your comminution equipment.
Introduction to physics-based models
Check the video
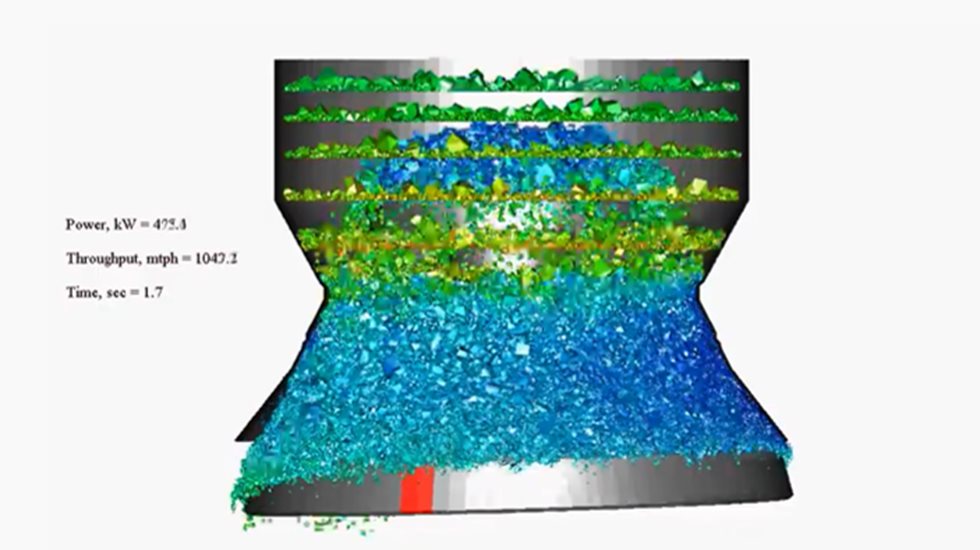
00:00
Simulation of primary, secondary and tertiary crusher
Primary secondary and tertiary crusher simulator
The simulator tool is for design of crushers for optimal performance and energy efficiency
- Used for gyratory, jaw, impactor and cone crushers
- Applying Discrete Element Method (DEM) with particle breakage
- Prediction of power, throughput, particle size distribution and wear, for which the models have been validated with field data
- Uses non-spherical particles to ensure volume/mass conservation
Mill shell liner simulator
Designs mill liners with optimal performance
- Prediction of charge profile, power and energy spectra, liner wear life, which has been validated with field data
- Simulates various particle shapes including spherical particles and non-spherical ones like tetrahedra
Check the video
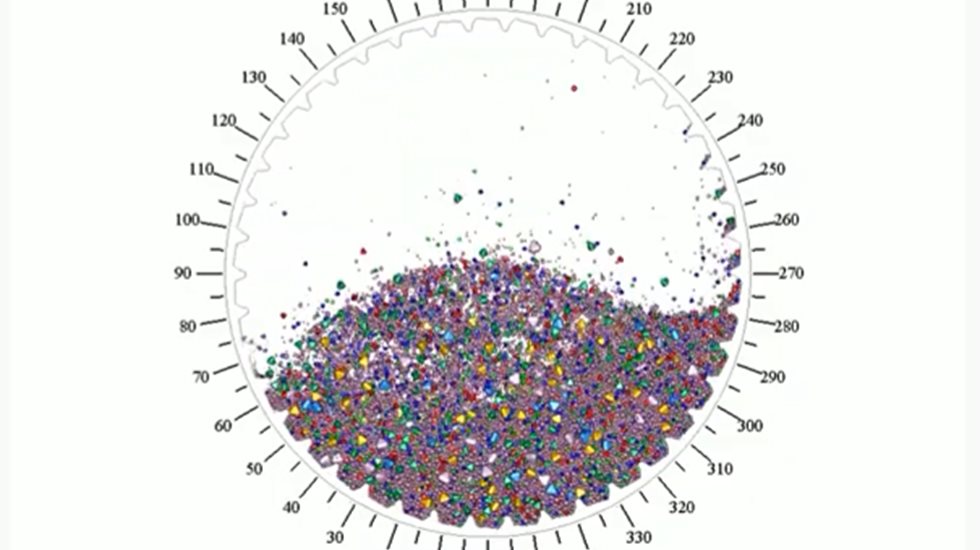
00:00
Mill shell liner simulator
Check the video
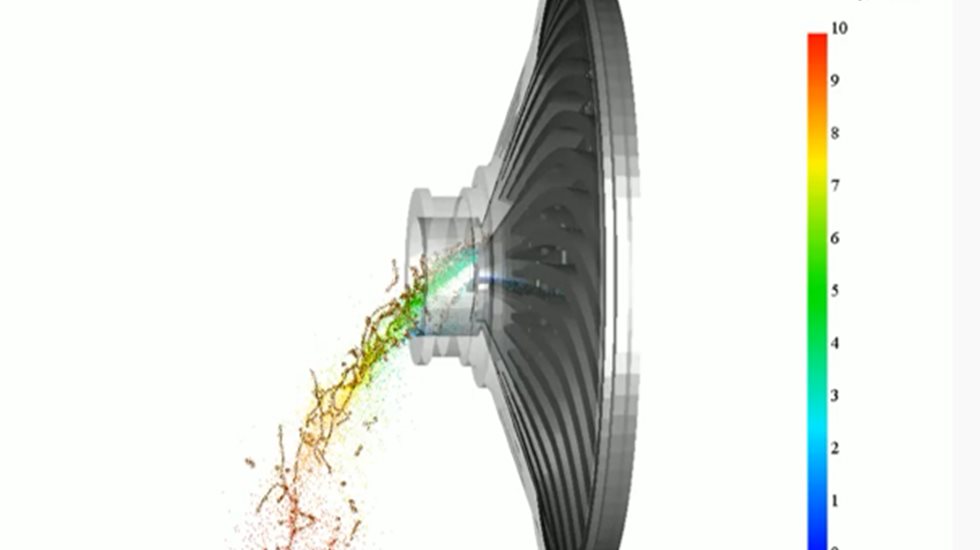
00:00
Mill flow-through-the-grates simulator
Mill flow-through-the-grates simulator
Enables design of mill discharge systems for optimal performance and energy efficiency
- Simulates mill discharge systems including the grates and pulp-lifters
- Prediction of discharge rates, hold- up in the pulp- lifters, power, and energy spectra, all validated with field data
- Comprehensive wear model validated with field data
Mill discharge simulator
Solution for evaluating optimal pulp lifter design configurations with pre-defined discharge rate
- Simulates flow profile, including flowback, carry-over, shear work at mill backend to determine how well any pulp lifter configuration works
- Comprehensive wear model validated with field data
Check the video
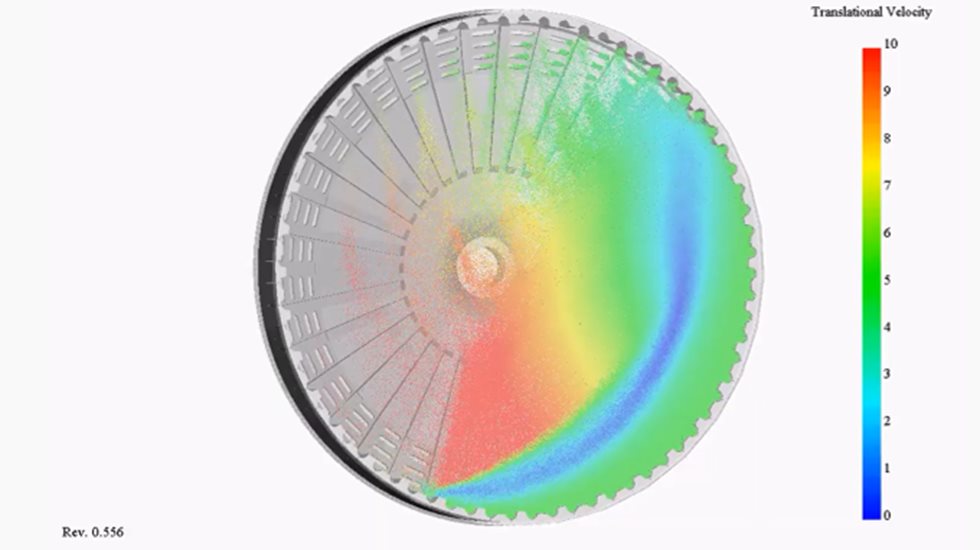
00:00
Mill discharge simulator
Check the video
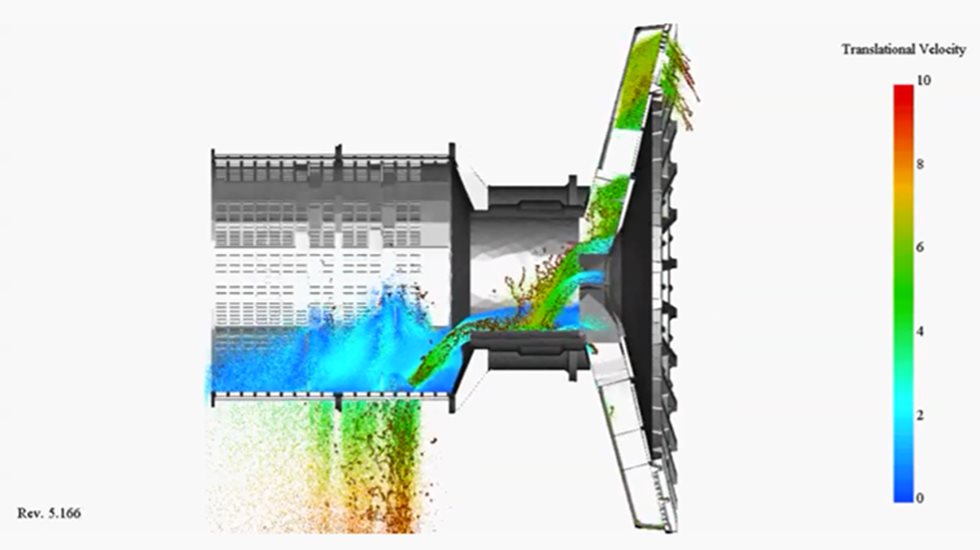
00:00
Mill discharge system with trommel simulator
Mill discharge system with trommel simulator
Designs the mill trommel for optimal performance
- Classification of discharge material on the trommel
- Simulates the effect of impact plate & dam height-position on the trommel performance
- Prediction of wear validated with extensive field data
Bulk material handling units simulator
Tool to design bulk material handling (BMH) units to capture particle flow characteristics
- Simulates chutes, conveyors, sizer systems, feeders, reclaimers
- Wear prediction validated by field data
- Effect of moisture incorporated in the model
Check the video
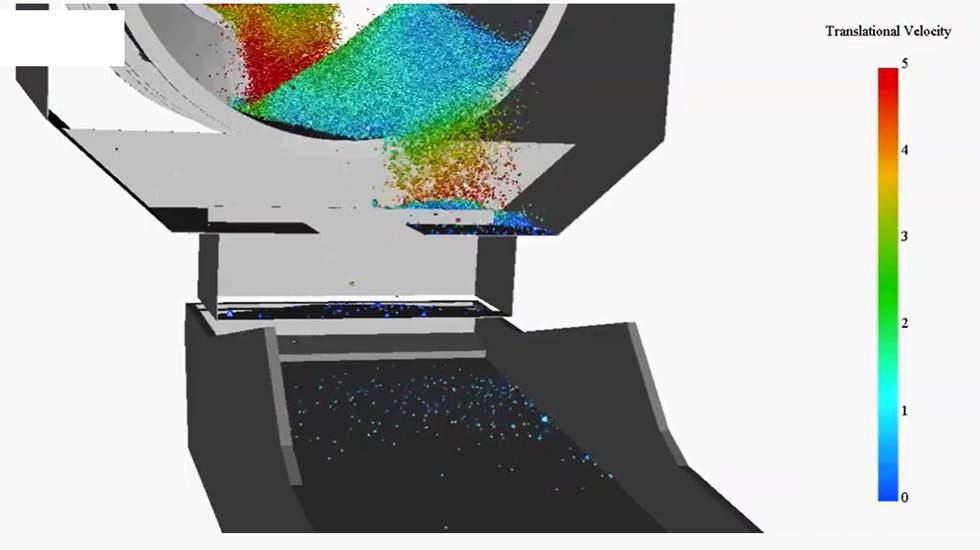
00:00
Bulk material handling units simulator
Check the video
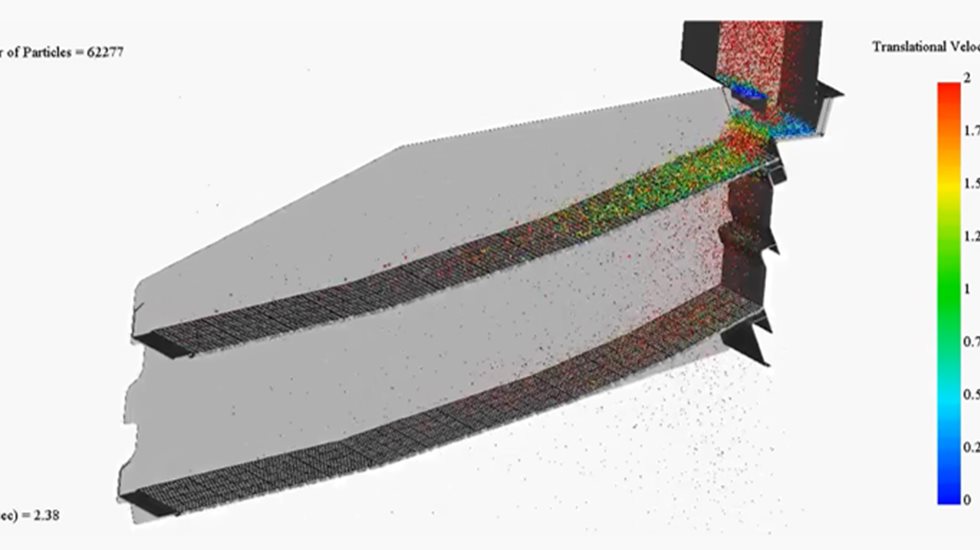
00:00
Screen simulator
Screen simulator
Designs screens for optimal material flow and mechanical performance
- Modelling various screen types & motions including multi-deck screens, with elliptical, linear and circular motion
- Simulation of material flow through each screen panel
- Realistic prediction of material classification
- Bed depth and particle speed predictions
HPGR physics-based performance calculator
Designs full scale HRC™ HPGR for optimal performance and energy efficiency
- Combines the physics of the machine, process dynamics, and lab-scale ore characterization data
- Mechanics of the HPGR is represented by a plastic rolling resistance model and based on Packed Bed Test (PBT) stress-strain and cake density relationships
- Prediction of gap, PSD, throughput, and power over a full range of operating conditions
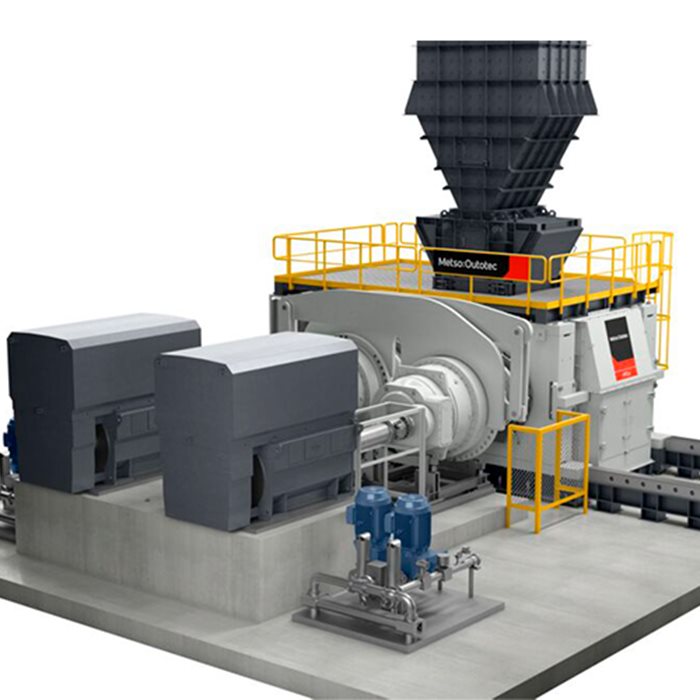
Check the video
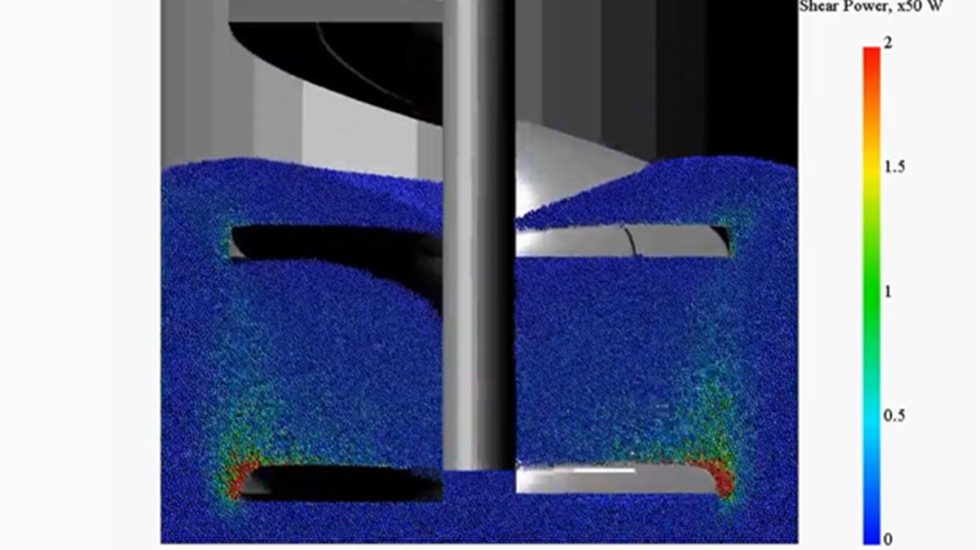
00:00
Vertimill simulator
Vertimill simulator
Designs Vertimill liners
- Prediction of liner wear life, power and energy spectra validated with field data
- The code implementation is flexible such that constraints, manipulated/controlled variables can be added to mimic the real-life operating practices - automatically adds media in order to keep the power constant