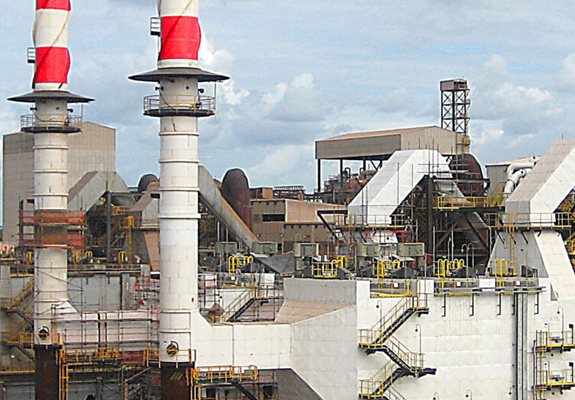
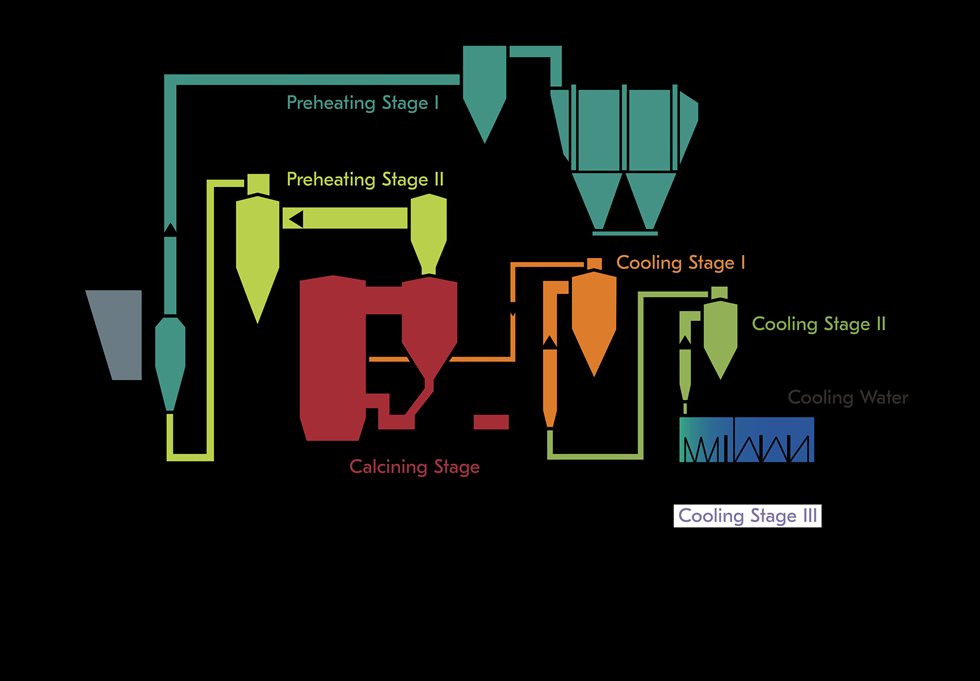
Supporting your operations, from plant design expertise to equipment, parts and services for every stage of your process.
Are you looking to increase production, reduce risks, lower operating costs and enhance environmental performance? Then you are in the right place.
From the design and supply of products for a greenfield plant, to the addition of a single machine for an existing production line, we are here to help.
Rely on OEM experts because not all parts are created equal. Spare and wear parts built to perform.
Helping you get the most out of your equipment and processes.
Special/Chemical Grade Alumina’s are commonly used in a range of application, such as ceramics, refractories, glass, pigments and fillers, electronics and batteries, and as abrasives and polishing agents. The production of these materials require calcination at higher temperatures than what is used to produce Smelter Grade Alumina (SGA), and often also the use of mineralizers. By adjusting calcination parameters, mainly calcination temperature and retention time some of the key properties can be controlled to meet required product quality specifications.
Metso has developed a flexible dual purpose CFB calciner design, suitable for production of chemical grade alumina as well as SGA. The main components of the Circulating Fluidised Bed (CFB) calcination process are: two preheating stages, a calcining stage and two cooling stages. Smelter Grade Alumina (SGA) CFB calciners typically operate in a range from 900 to 1000°C, depending on product quality targets. However for Chemical Grade Alumina temperatures, an excess of 1100°C are required. With Metso’s calcination technology the temperature setpoint along with furnace inventory can simply be adjusted to meet the desired product quality grades. The temperature control is very precise and the temperature is very uniform throughout the reactor allowing a homogenous product quality to be achieved.
The CFB calciner makes use of a multi-stage venturi preheating system to recover the waste gas heat by preheating and drying the feed prior to reaction. The main calcination reaction is carried out in the CFB reactor. The energy for the calcination process is supplied by direct combustion of either oil or gas. Energy in the hot alumina is also recovered in a multistage cooling system (which includes a pair of cyclones and a fluidized bed alumina cooler). Another option for further energy recovery is to include a “feed dryer” in the arrangement. This unique and proven piece of equipment utilizes heat from the fluid bed cooler to pre-dry a part of the feed stream before it enters the calciner. The first cooling stage can also be designed to be operated as a flash reactor, raising the temperature to 1400-1600 °C thereby enabling the production of more highly calcined products in the same equipment.
The CFB technology can be scaled up without consequences for product quality owing to the recirculation of solids in the CFB, which results in an even temperature distribution and homogenous product quality also at large capacities and during load changes. The efficient use of heat exchange technology reduces the total energy consumption significantly compared to other technologies.
Another key feature with the CFB calcination technology is the low emissions. Due to the unique flameless in-bed combustion system in the CFB reactor, and the recirculation of hot solids and resulting uniform temperature profile throughout the reactor system, the generation of thermal NOx can be kept at a minimum. The application of a staged combustion air supply and vigorous mixing of air, fuel and solids minimizes the formation of CO. State of the art ESPs are used for final dedusting of the off gas, in order to meet the local environmental limits.
Feed Material
The chemical grade alumina calciner is very flexible with regards to feed material properties. The feedstock can be either a precursor alumina or an aluminium hydroxide (boehmite, gibbsite, bayerite). The calcination plant is also flexible with regards to feed moisture. The particle size of the feed should ideally be in the range of a D50 from 50 µm up to 1000 µm to allow efficient fluidization and solid gas separation in cyclones and other equipment.
Product Qualities
One of the main advantages of Metso’s Special and Chemical Grade Alumina Calcination Plant solution is the operational flexibility and the fact that key processing parameters, such as temperature and furnace inventory, can be precisely controlled and in a broad range. Furthermore, the alumina quality achieved is largely plant load independent, meaning that the target quality grades can be achieved also at reduced plant load.
Without the optional flash calcination stage, the calciner can achieve alpha alumina contents in the range of 30-40 wt-% (corresponding to a BET of 30-35 m2/g). With the optional flash calcination stage in operation, alpha alumina content up to 60-70 wt-% can be achieved (corresponding to a BET of approximately 20 m2/g). Note that alpha alumina formation, LOI and BET are influenced by impurity content (soda and others) as well as the use of mineralizers. For higher alpha alumina content, lower BET or LOI, or coarser feed material Metso can offer rotary kiln based solutions. Metso has extended pilot plant and laboratory facilities for testwork on conversion and fluidization behavior, which are utilized in the plant design phase to derive key design and scale-up parameters. This ensures that product quality and performance targets can be met.