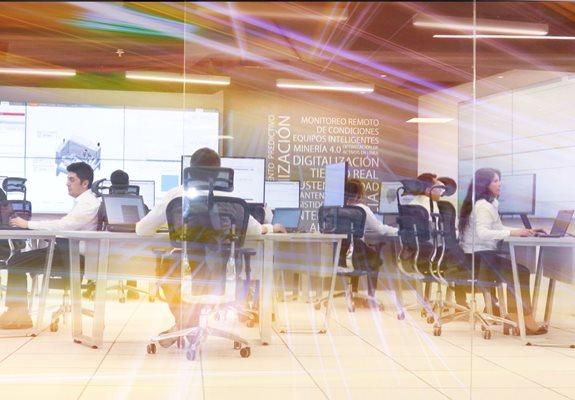
Connected equipment and remote expert services to help you reach your targets
Predict and prevent to get ahead of issues before they start
Gain access to our experts with recommendations and assessments using real-time analytics
Identify and sustain continuous development and performance through proactive collaboration
Optimize your process and improve realibity
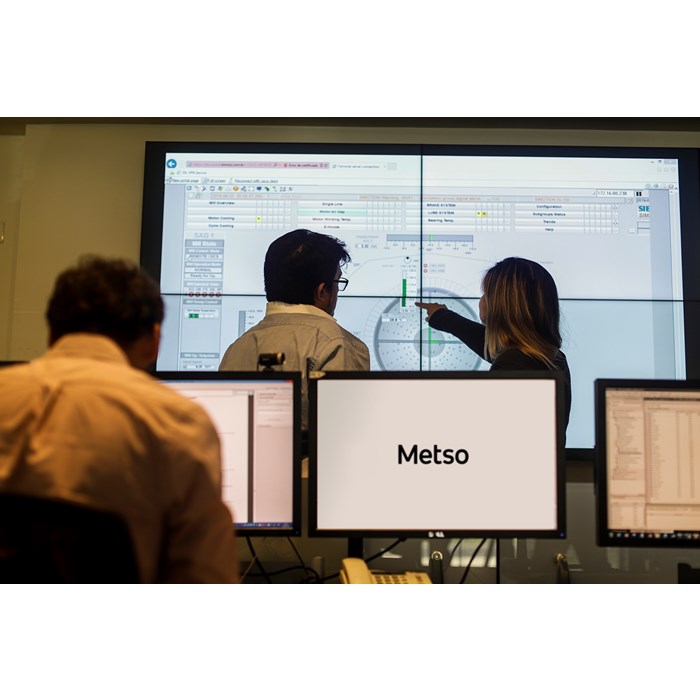
- State-of-the-art facilities custom-built for collaboration
- The highest level of cybersecurity
- Services for both Metso and non-Metso equipment
- Data-driven insights to complement and amplify the performance of Metso services and products
Performance Centers service offering
Real-time visibility
Real-time equipment information and alarms through Metrics Monitoring for enhanced planning and decision-making. Learn more here>>
Expert monitoring and recommendations
Performance Centers use advanced digital tools and the global expert network of Metso to provide a holistic expert remote service. We help to improve the reliability, operational performance, and optimization of your equipment based on your targets and needs. Learn more here>>
Sustaining Performance – Advanced Process Control and Intelligent Instrument Lifecycle Services
Maintain the performance of your Advanced Process Control or intelligent instruments at the high level where it is first, right after commissioning with these lifecycle service solutions.
Remote maintenance support for gearless mill drives
Specialized technical assistance as well as proactive and emergency support on and off-site.
Reliability, maintenance and process optimization
Integrated, performance-based solutions combining expert services on sustainability, Performance Centers, reliability-centered maintenance, process optimization, and advanced process control.